
TECHNOLOGY IS ESSENTIAL TO MANAGE MEGA PROJECTS
Shailendra Kumar Patel
Deputy General Manager (Planning), Heavy Civil Infra IC
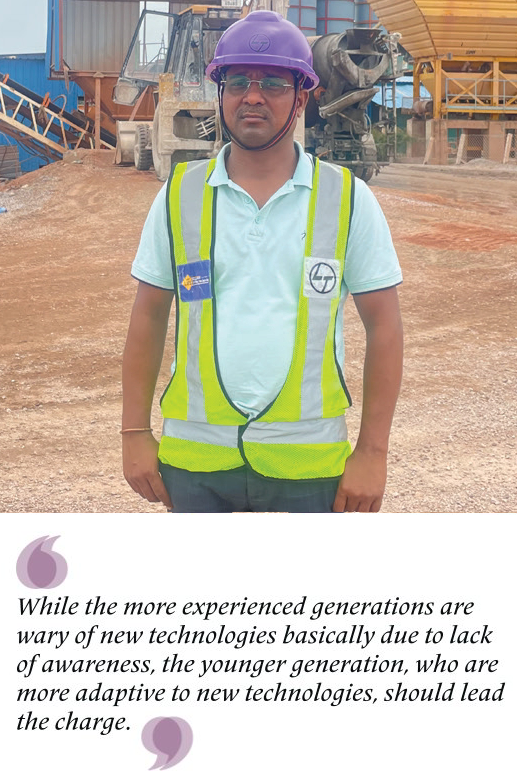
Having worked at the MAHSR C4 package since September 2021, Shailendra Patel is convinced that technology is vital to handle mega projects. “Here, I take care of concrete production and coordinate with the site team to meet the daily requirements of concrete from the batching plants located at various locations in Section 5 on the 60 km Bharuch–Vadodara stretch,” he shares. “Delivering concrete at various locations from different locations simultaneously using Transit Mixers in a linear (concrete structure based) project is extremely challenging, and it is digitalization that has helped us succeed.” He adds that with the adoption & implementation of ConEase & 100% IoT in concrete production, the team can track orders and maintain structure ID–wise records.
He is happy that his Project Director, C Shivakumar, is someone with great affinity for digitalization, which motivates everyone to adopt and implement it in every process of daily activities. “His motto is to work smartly and stay calm and cool, for which digitalization is the key,” says Shailendra, who is on familiar territory having implemented the Trimble – 2D system in graders at one of his previous sites, the Rewa–Katni–Jabalpur–Lakhnadoun Road Project. “It enabled us to prepare the layer work for earthwork/ GSB, etc. much quicker and cost-effectively. It has since been upgraded to a 3D system and is being used at every road project site of TI IC,” he says with a look of achievement.
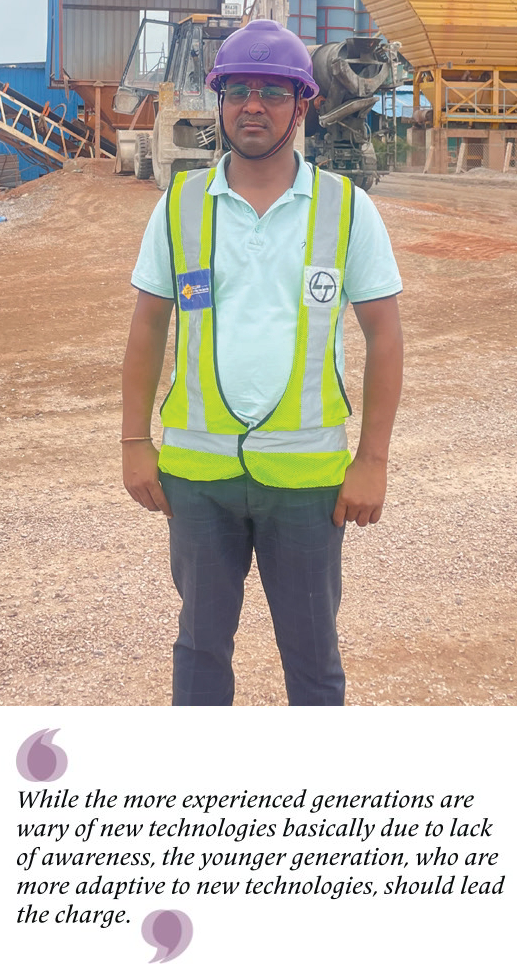
Having worked at the MAHSR C4 package since September 2021, Shailendra Patel is convinced that technology is vital to handle mega projects. “Here, I take care of concrete production and coordinate with the site team to meet the daily requirements of concrete from the batching plants located at various locations in Section 5 on the 60 km Bharuch–Vadodara stretch,” he shares. “Delivering concrete at various locations from different locations simultaneously using Transit Mixers in a linear (concrete structure based) project is extremely challenging, and it is digitalization that has helped us succeed.” He adds that with the adoption & implementation of ConEase & 100% IoT in concrete production, the team can track orders and maintain structure ID–wise records.
He is happy that his Project Director, C Shivakumar, is someone with great affinity for digitalization, which motivates everyone to adopt and implement it in every process of daily activities. “His motto is to work smartly and stay calm and cool, for which digitalization is the key,” says Shailendra, who is on familiar territory having implemented the Trimble – 2D system in graders at one of his previous sites, the Rewa–Katni–Jabalpur–Lakhnadoun Road Project. “It enabled us to prepare the layer work for earthwork/ GSB, etc. much quicker and cost-effectively. It has since been upgraded to a 3D system and is being used at every road project site of TI IC,” he says with a look of achievement.
At another of his previous sites, the Bar–Bilara–Jodhpur Road Project, Shailendra and team used sensors in soil compactors while carrying out earthwork in earth retaining structures to safeguard the RE panel structure from being hit by soil compactors (especially in the night). For better control on the production and delivery system, he recommends the integration of production and delivery systems onto one platform, with its own complete navigation system in a linear project.
“While the more experienced generations are wary of new technologies basically due to lack of awareness, the younger generation, who are more adaptive to new technologies, should lead the charge,” says Shailendra, convinced that the rest will follow once they see the benefits and ease of doing things using new technology.
On his personal front, this native of Rewa, Madhya Pradesh, is married to Seema, a homemaker, and they are blessed with three children: twin sons, Shashwat & Sarthak, and a daughter, Bhavya. “I love to listen to and sing old songs, do gardening, and play chess & cricket,” he laughs.
Being a civil engineer, joining L&T has been a dream come true. Another memorable day is the birth of his daughter.
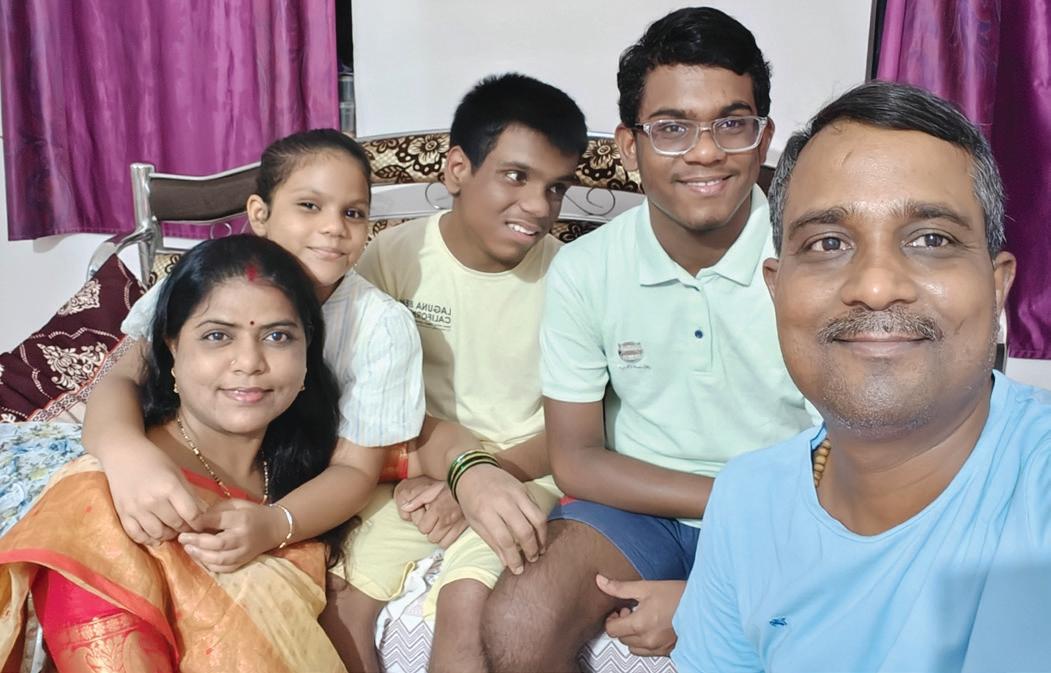
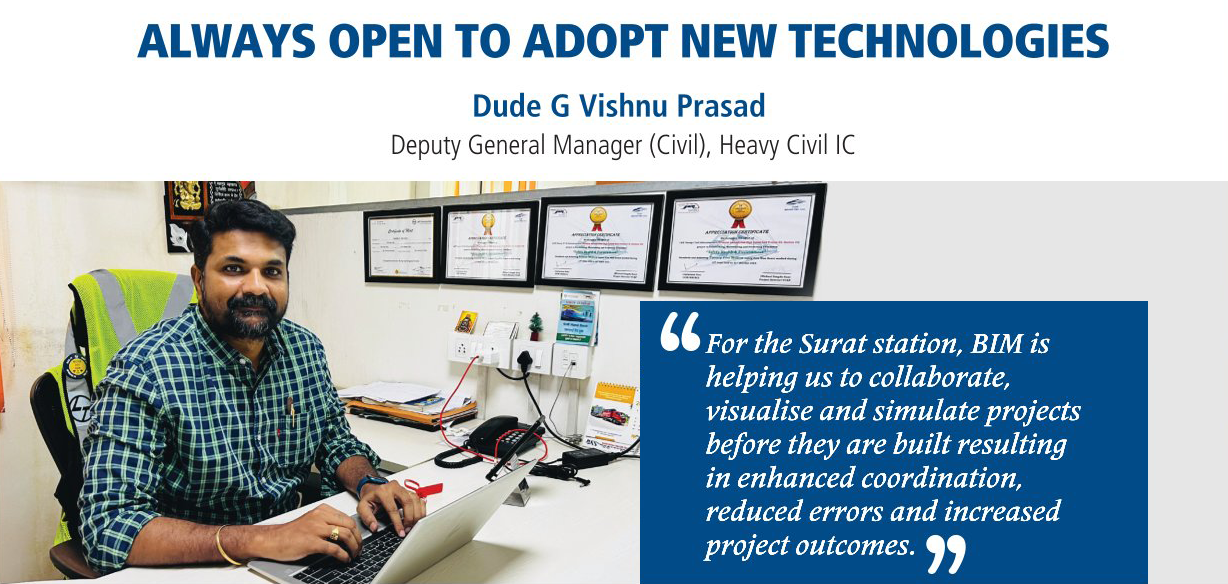
“I always look to adopt new technologies which are more productive and easier to execute and monitor,” declares Vishnu Prasad, who throughout his tenure with L&T at various projects like L&T HEW – Hazira, Technology Park (Phase 1) – Baroda, VSF Unit – Grasim Projects, GHB Valsad, APTIDCO Housing – Tiruvuru, and currently at his present assignment at the MAHSR C4 – Section 3, has enjoyed opportunities to work with technology.
“In the APTIDCO projects, we digitized formwork and finishing material by fixing barcodes on components to track better and utilize material faster improving our productivity and material reconciliation,” he shares. “Here, for the Surat station, BIM is helping us to collaborate, visualise and simulate projects before they are built resulting in enhanced coordination, reduced errors and increased project outcomes.” In addition, Vishnu mentions drones for progress monitoring, & VR for safety inductions and project briefings.
Referring to the challenging diamond-shaped Surat station structure, he shares, “to get that profile, we designed the column of size 1.5 × 1.5 m in a Rhombus shape and decided to cast the columns using 7.2 m high formwork by fabricating some non-standard items.” Again, for the Surat station, they have introduced a sprinkler system to cure 50 × 45 m slabs that has won appreciation from the Client and the Japanese teams, he adds happily.
At a project of the magnitude of MAHSR, one of the team’s biggest challenges has been interfacing and Vishnu enumerates several steps they are taking to address this issue of identifying interface, defining responsibilities, improving communication & collaboration, and using interface management tools like BIM.

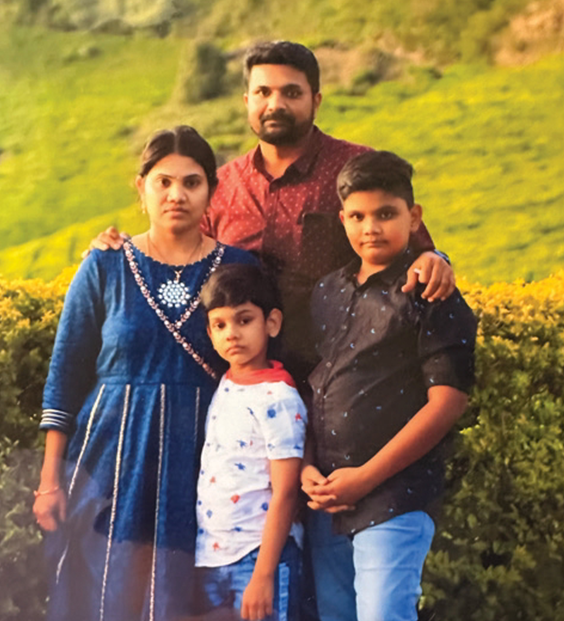
As part of his technology wish list, he would like to introduce wearable technology in the construction industry to improve productivity, health, and safety and AI for tasks like predictive analytics, risk assessment, and project management.
“My seniors and team members have been most supportive in my effort to adopt new technologies at site,” he says earnestly. “One thing that I like most about L&T is the support that we receive from the management to grow individually which helps the organization to grow as well.”
Hailing from Amalapuram, Andhra Pradesh, Vishnu’s better half is Ramya, a homemaker, and their family is complete with their two children, Sathwik & Rishikesh. His favourite pastimes are playing cricket and listening to music.
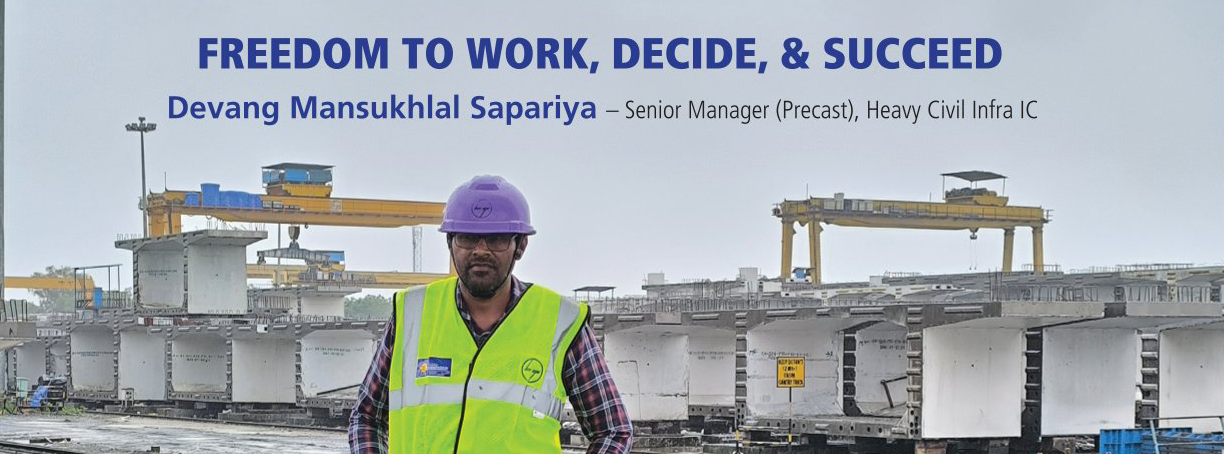
Nothing is more satisfying for an engineer handling precast activities when his team achieves a milestone. Devang Sapariya experienced that ‘high’ at the MAHSR project when the team casted 100 segments in February 2023. “It was the happiest day of my career and even of my life,” he laughs delighted, “and it was a proud moment for me when all my seniors appreciated our achievement and applauded us at our monthly meeting.”
Although at his first project with L&T, Devang brings with him the experience of having with various construction companies on a variety of challenging projects. Presently, he finds himself at undoubtedly the biggest construction project being executed in the country and enjoying the opportunity to work on some unique technologies. “One such is the unique FSLM or the Full Span Launching Method which is an advanced version of the SBS or Span-by-Span launching method,” he explains. “It is faster too, for while we were able to cast 100 spans over 2 years with the SBS method, with FSLM we are able to achieve the same number in just 18 months, saving 6 months for the project,” he says with a punched fist.
Productivity in a casting yard is completely dependent on labour. “Mainly there are four activities that require precision which are outer shutter fixing, cage lowering, bulkhead fixing, and inner fixing and all these four activities depend upon labour,” Devang informs. “Of course, we can reduce labour involvement by providing a mechanical arrangement for the outer and inner shutter fixing.”
Is there some technological initiative that he would like to introduce? He nods vigorously mentioning that he would like to introduce a unique identification system in SBS with barcode tagging. “We can fix one barcode in each segment which carries all data like date of casting, 7- and 28-day cube strength reports, mix design used, quantity of steel used, all the checklists, names of engineers involved in casting, record of prestressing and many more.” He pauses for a moment to think whether he has missed something and then adds, “This will be helpful to the client after handing over of project, with all details available in one click,” he snaps his fingers.
A native of Jamnagar, Gujarat, Devang’s better half is Avani, a computer engineer & teacher, and their family is complete with their son, Paarth. He loves to drive to unwind.
“At L&T, I feel I have got the opportunity to play the role of a real engineer,” he says with immense commitment, “and I enjoy the freedom to work, take decisions on site with the support and valuable guidance of my seniors and succeed,” he signs off rousingly.

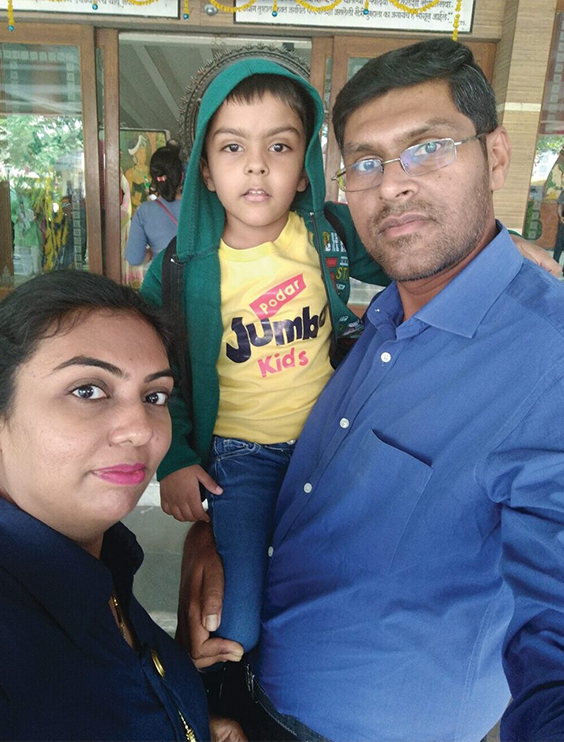

ENJOYING THE FRUITS OF
14 YEARS OF ALL-ROUND GROWTH
Mohit Gupta
Senior Construction Manager (Civil), Heavy Civil Infra IC
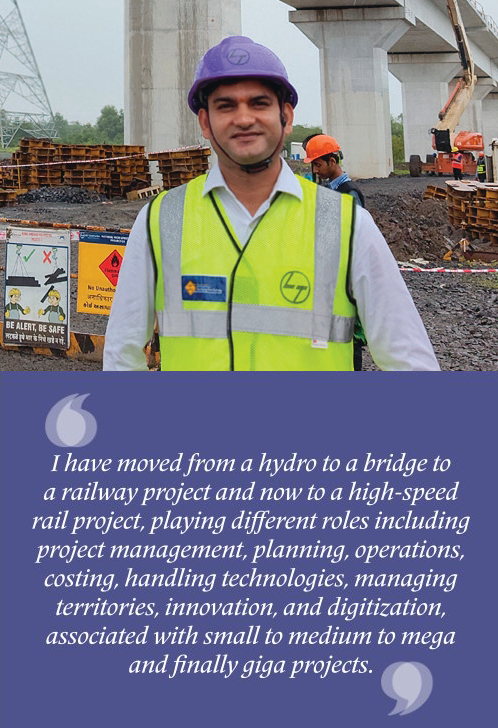
He could not have plotted his growth curve any better. A GET of batch 2010, Mohit Gupta joined the Srinagar hydroelectric project, then moved to the Barapullah Bridge project as Planning Manager, followed by a stint at WDFC CTP 1&2 and is presently at the MAHSR. “I have moved from a hydro to a bridge to a railway project and now to a high-speed rail project,” says Mohit, encapsulating his 14-year association with L&T, “playing different roles including project management, planning, operations, costing, handling technologies, managing territories, innovation, and digitization, associated with small to medium to mega and finally giga projects, with passion, hard work, and determination.”
“Several technological aspects implemented at MAHSR have started with my section at HSR,” he flags off, referring to full span casting of 970 T girders for the first time in India, using Henry Ford’s concept of division of labour and Apps to monitor every activity. “I have learnt to handle straddle carriers and bridge & launching girders, communicating with different stakeholders including the Chinese and Japanese,” he says. He has added a few key innovations like Modular USLG Trestles, sprinkling system in BP and Girder, rain sheds design and implementation in consultation with CMPC team, double head trailers for deck furnishing works and backfilling with crushed sand to save cost and time.
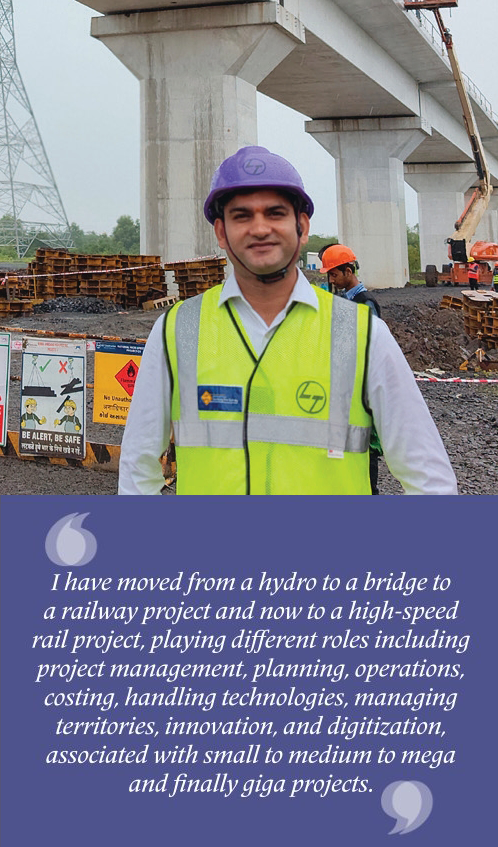
He could not have plotted his growth curve any better. A GET of batch 2010, Mohit Gupta joined the Srinagar hydroelectric project, then moved to the Barapullah Bridge project as Planning Manager, followed by a stint at WDFC CTP 1&2 and is presently at the MAHSR. “I have moved from a hydro to a bridge to a railway project and now to a high-speed rail project,” says Mohit, encapsulating his 14-year association with L&T, “playing different roles including project management, planning, operations, costing, handling technologies, managing territories, innovation, and digitization, associated with small to medium to mega and finally giga projects, with passion, hard work, and determination.”
“Several technological aspects implemented at MAHSR have started with my section at HSR,” he flags off, referring to full span casting of 970 T girders for the first time in India, using Henry Ford’s concept of division of labour and Apps to monitor every activity. “I have learnt to handle straddle carriers and bridge & launching girders, communicating with different stakeholders including the Chinese and Japanese,” he says. He has added a few key innovations like Modular USLG Trestles, sprinkling system in BP and Girder, rain sheds design and implementation in consultation with CMPC team, double head trailers for deck furnishing works and backfilling with crushed sand to save cost and time.
His list of tech interventions is long: TILOS, BIM, Procube, ConEase, Rebar Pro, WMS, RFID fuel tagging, SHEILD, Material Nxt, and geospatial. “I am grounded but feel that we can do much more with accurate data for technology to play a more effective part,” he points out. “As an organization, we have matured to implement digital tools, and technologies like AI can help leaders to take more informed decisions, speed up actions, and ultimately empower us to deliver our projects faster.”
Mohit attributes his impressive growth in large measure to the vision and support of the leadership and team. “I am blessed to be directly guided by Mr Rakesh Kumar Jha, in project execution and planning, and have learnt expertise in execution from Mr. Zamshed Ali.” He extends his gratitude to TFL, G Vinod, Sanjeev Gupta, Navneet Kaul, TSRM Srinivas, GB Rao among others for the knowledge he has gained.
Though from Alwar, Rajasthan, Mohit has been brought up in Chandigarh, where he did his schooling, engineering, MEP from IIMA, and leadership from IIMN. Presently, he is in Navsari, Gujarat, with his wife, Shelly Gupta; mother, Maya Gupta; and his two lovely kids, Ayaan and Yuvaan. “My wife was a schoolteacher but is now a homemaker, taking care of my mother, kids, and me,” he smiles. “My hobbies are listening to music, singing, reading books, walking, watching, and playing cricket,” he reveals the full life he enjoys.
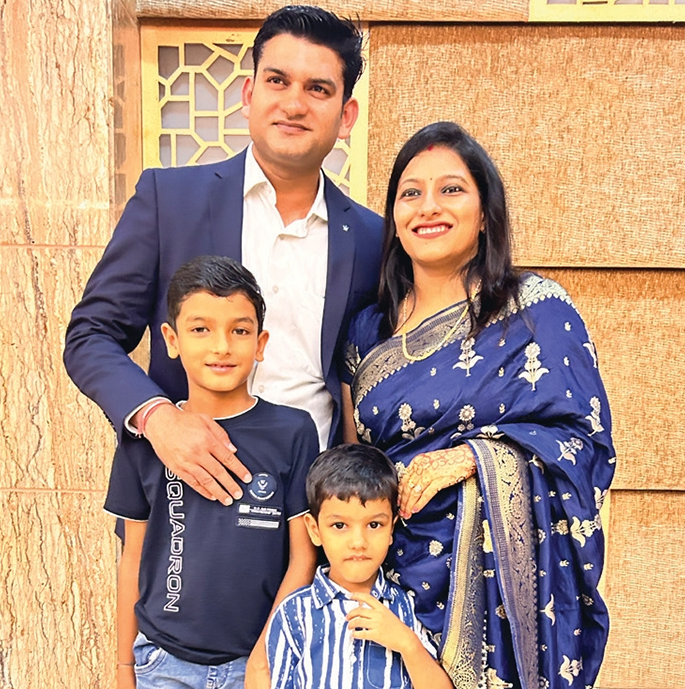

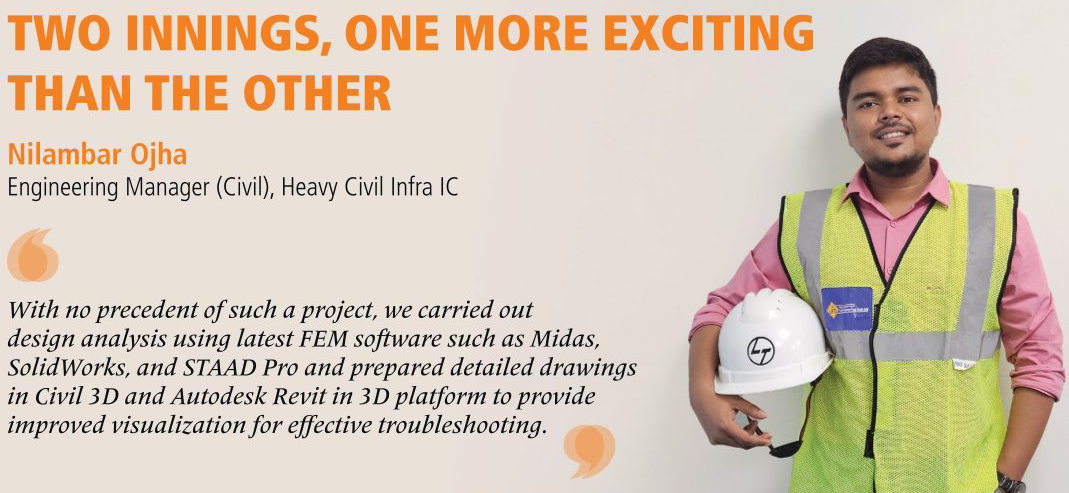
A GET of batch 2013, Nilambar Ojha worked on the iconic DFCC project in Rajasthan & Gujarat during an initial 7‑year stint. “I led the design team, achieved 98% design, drawing approval for the project length, and earned a Remarkable Appreciation Letter from the Chief General Manager of DFCCIL Vadodara,” he recalls proudly. On rejoining the fold in 2021, he is working on the equally celebrated MAHSR project, in the CMPC department, responsible for Sections 2 & 4 and leading a team of 6.
“I have always been driven by technology and am dedicated to implementing the latest innovations for project advancement,” he says with vigour, and enjoying several opportunities at C4 to live his passion. “Innovation isn’t just about new ideas but about tailoring solutions to meet unique challenges. Every design, methodology, and system I’ve developed with senior guidance stand as testaments to the power of customization in engineering excellence,” he says with gravitas.
Setting up one of India’s largest Precast Manufacturing Hubs to make the millions of elements for the noise barriers, cable ducts, and duct slabs is an outstanding achievement. “It is equipped with an automatic concrete distribution system and an automatic battery mould,” he says, flagging off that the Hub presently produces 500 noise barriers and 300 cable ducts per day and is capable of reaching up to 1200 elements per day. “We won the 1st Runners’ Up prize in the Project category at the Pi Awards 2023,” he adds with elan.
Other standout introductions are an innovative, comprehensive Deck Furnishing Solution to complete 2 million deck furnishing elements, which has won a 2024 Pi Award under the Project category, and an advanced Robotic Rebar Cage Manufacturing unit (RRCM) to fabricate noise barrier rebar cages to reduce dependency on labour and ensure effective task completion with zero rejections and fatalities.
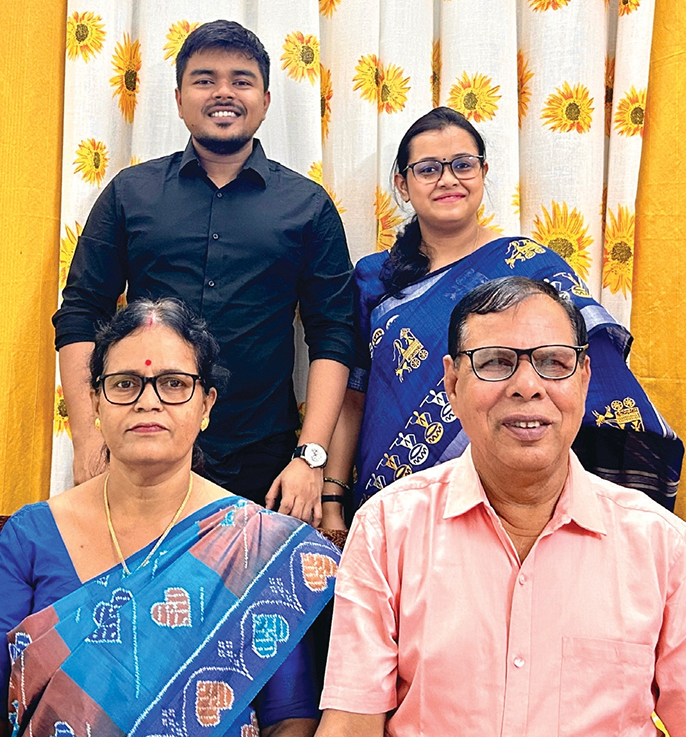

“With no precedent of such a project, we carried out design analysis using latest FEM software such as Midas, SolidWorks, and STAAD Pro and prepared detailed drawings in Civil 3D and Autodesk Revit in 3D platform to provide improved visualization for effective troubleshooting,” shares Nilambar, “We have also conducted several digital workshops on 3D platforms to develop the skills of fabricators.”
To keep the tech fire burning, Nilambar advocates stronger partnerships with technology providers and innovators & greater use of AR & VR. “Currently we are working closely with LTI Mindtree to develop AI based technology solutions,” he adds.
Hailing from Siliguri, West Bengal, Nilambar is married to Deepsikha Barua, a Bank Manager in Punjab National Bank, Surat. Cooking and driving are his hobbies and a moment to cherish was the joy in his parents’ eyes when he presented them with his first salary.
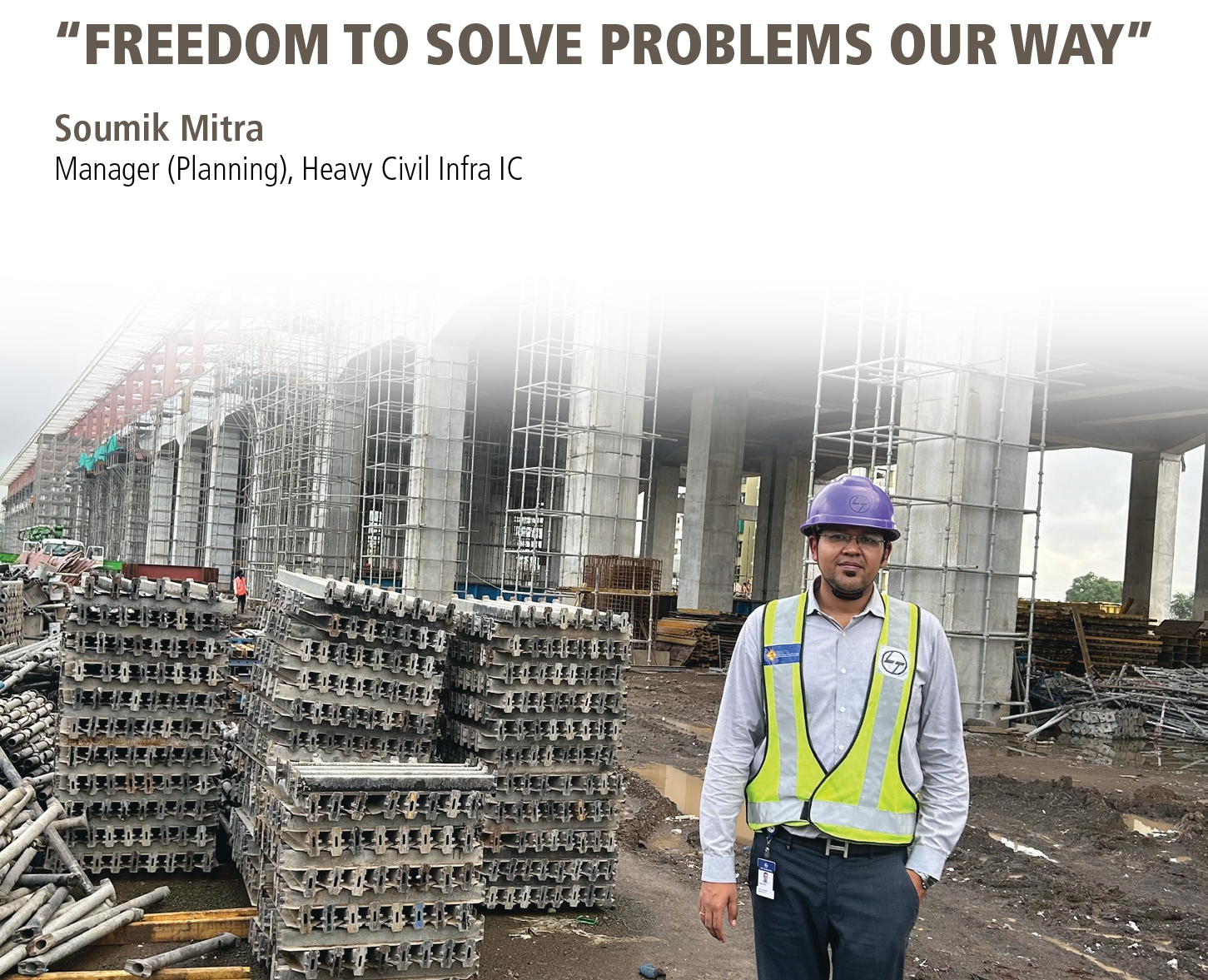
Although Soumik Mitra has worked on several important projects with other construction companies, he is proud that his first with L&T is the iconic MAHSR project. A lateral, what has impressed him most about L&T is “the freedom to pursue solutions to problems our way that gives us an exceptional platform to create unique tailored, innovative, and specific solutions for problems and I am keen to inculcate this USP in myself,” he says purposefully. “This empowerment, I believe, is very important in a project-based industry, as every job is unique, in some ways similar yet different,” he remarks knowledgably.
Soumik has several opportunities to work with technology like using drones to monitor a 53-km stretch, TILOS for a better visualization of schedules, and the Oracle-based Unifier, implemented by the employer at enterprise level to readily access contractors, consultants and vendor documents. “We use two in-house developed digital tools: Geofreq and an FSLM tracker,” he shares. The first is a tunnel instrument monitoring software, and the tracker captures data to provide insights into the various activities connected to full span girder casting.
“One major challenge I faced was to accurately forecast timelines for full span girder casting and erection and with no historical data available, we had to establish the cycle time,” recalls Soumik grimly. “Initially I detailed out all the activities to prepare an initial expected cycle time and then with an App-based FSLM tracker sheet monitored activities, which made data collection, analysis, and visualization quick and easy. We established the cycle time and can course-correct and even confidently forecast now,” he exults.
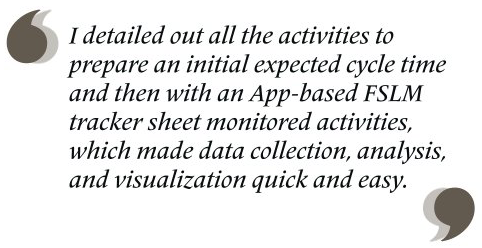
BIM models have been generated for both the Vapi Station and the mainline viaduct, which are helping the team to monitor progress and make 3‑month projections, but Soumik feels that more can be done with BIM other than just 3D visualization, starting from preliminary drawing to integrating every revision, scope management and change, linking them to schedule to create an integrated ecosystem in the BIM model for scope and schedule management.
All praise for the support to implement digitalization, he flags off for special mention Project Director, R. K. Jha; TFL, G. Vinod; A. L. Sekar; S. Mohanbabu; and a host of others.
A native of Ranchi, Jharkhand, Soumik’s wife, Sneh, is currently on a sabbatical to take care of their 4‑year-old son, Shourya, is a law graduate having cleared the State bar and worked earlier as law research associate at the National Company Law Tribunal, Kolkata and as Associate Legal Counsel for the Government of Jharkhand at the Jharkhand High Court. To relax he loves to play badminton and travel and remembers a lovely Goa trip.

WELCOME TO SPEED & SCALE
Vivek C Tank
Manager (Planning), Heavy Civil Infra IC

His previous experience with other construction companies on important projects could not have prepared Vivek Tank for the speed & scale at the MAHSR, his first with L&T, where he admits that he has been privileged to be involved with several unique technological and digital initiatives.
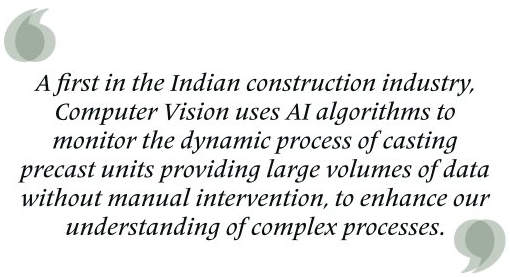
When dealing with nearly 1,00,000 MT of PT works in almost 90 lakh RMT of HDPE ducts, reducing wastage can be huge winner. “We identified, evaluated, and employed four prestressing agencies, separated the wastage from the quoted price to finalize rates by calculating the individual wastage for each agency based on their prestressing system,” explains Vivek. “Wastage was counted down to the last millimetre to eliminate any excess,” he stresses. The result is 1% saving in wastage that translates to nearly 1,000 MT in material savings.
By persuading suppliers to provide tendons in required cut lengths for round and flat ducts, installation time & wastage have been significantly reduced. “In fact, it is a win-win situation,” smiles Vivek, “for suppliers find it more convenient to transport double the quantity of specialized cut lengths, in the same truck load.” Another winning move by the team was to set up a precast factory for which they won a PI Award, that Vivek describes as a highlight and a culmination of innovation across many different processes. “It involved planning, developing, and implementing technology for a factory capable of producing 5,00,000+ precast units by integrating systems like concrete distribution, battery moulds, steam curing systems, automatic temperature monitoring system and run-off tracks.”
To hit desired time cycles given that 40% of the project’s volume is related to precasting, Vivek has been involved in developing an online precast activity tracker that records 30 distinct activities for casting full span girders and 39 for the erection process. He is elated with his role to develop an App, ‘A‑Eye’, to digitally capture qualitative & quantitative data for 5 lakh+ precast units. “A first in the Indian construction industry, Computer Vision uses AI algorithms to monitor the dynamic process of casting precast units providing large volumes of data without manual intervention, to enhance our understanding of complex processes,” he notes.
Vivek considers the development & implementation of technological initiatives as an ongoing journey, crediting the project leadership for its success. “They’ve trusted us, provided a platform, and enabled us with resources to become tech champions. Their continuous guidance and support are crucial to steer us on this path.”
A ‘Surati’ by birth, he is immensely proud that his project runs right through his hometown. Vivek’s better half is Neha Vegad, working as a recruiter with a private firm. He loves to travel when free and enjoys a perfect work–life balance.
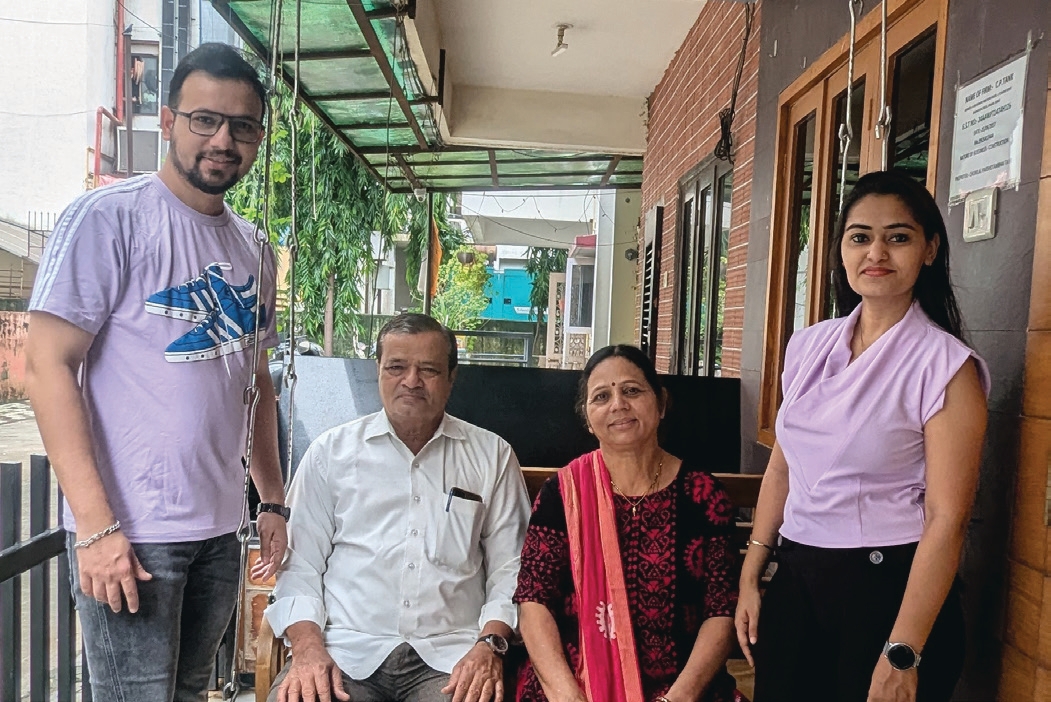